OUR SAVOIR-FAIRE SINCE 1958
One of the most delicate factors to comprehend is the growth aptitude of this tree. And there, where neighbouring trees such as the pine or even the oak grow fairly rapidly, the Olive tree requires a greater number of years to develop. Due to its new shoots the Greeks baptised it as immortal further to the fire in the temple in Athens.
This is the reason why all my work is orientated towards saving and economising this very noble raw material.
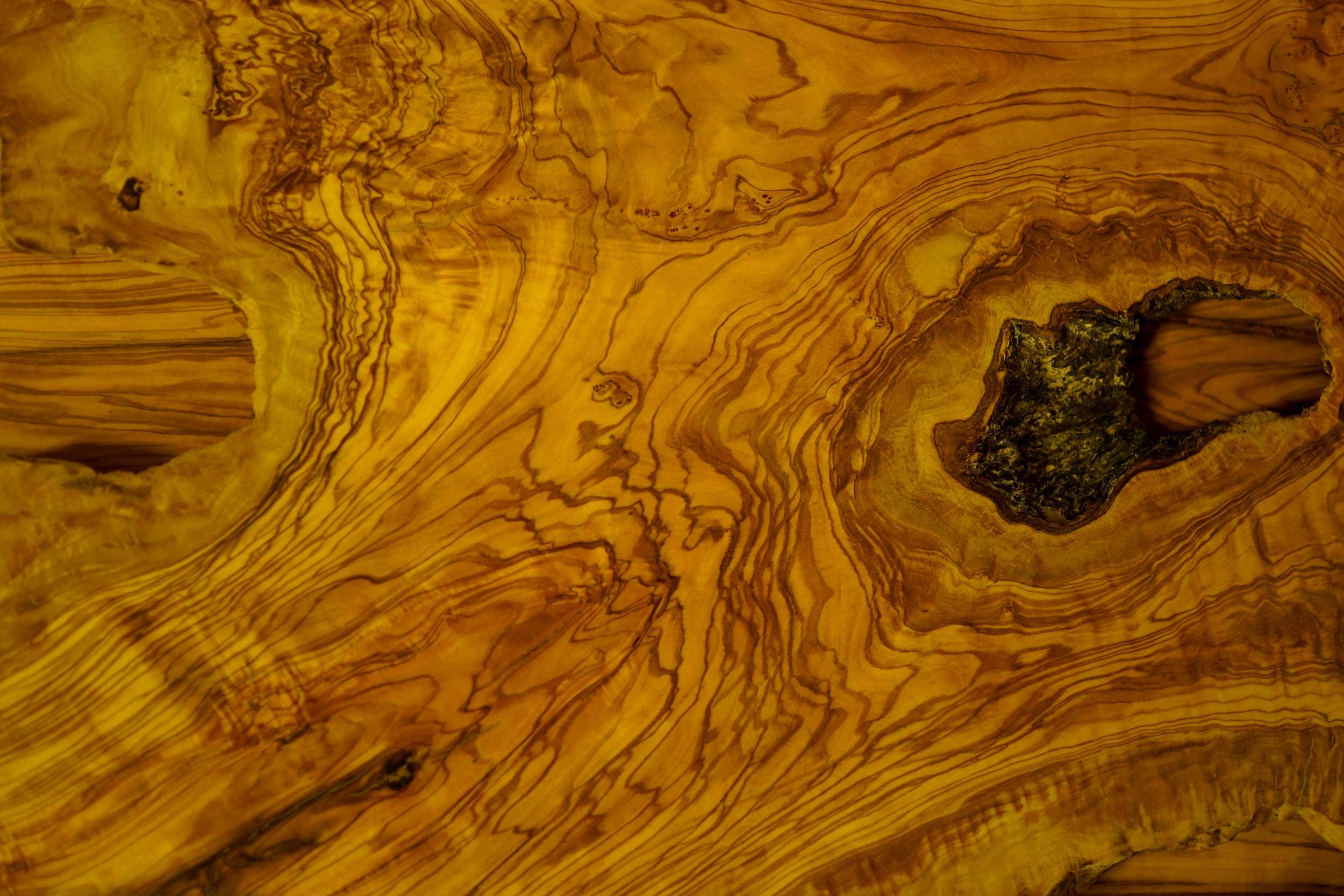
One of the most delicate factors to comprehend is the growth aptitude of this tree. And there, where neighbouring trees such as the pine or even the oak grow fairly rapidly, the Olive tree requires a greater number of years to develop. Due to its new shoots the Greeks baptised it as immortal further to the fire in the temple in Athens.
This is the reason why all my work is orientated towards saving and economising this very noble raw material.
To start with I need to find quality trees because not every Olive tree has necessarily interesting wood to work on.
I recuperate the branches, stumps, or trunks, that are also known as olive logs, in various countries such as France, Spain, Italy and sometimes even further afar, according to the hazards of climates (for example damage caused by frost).
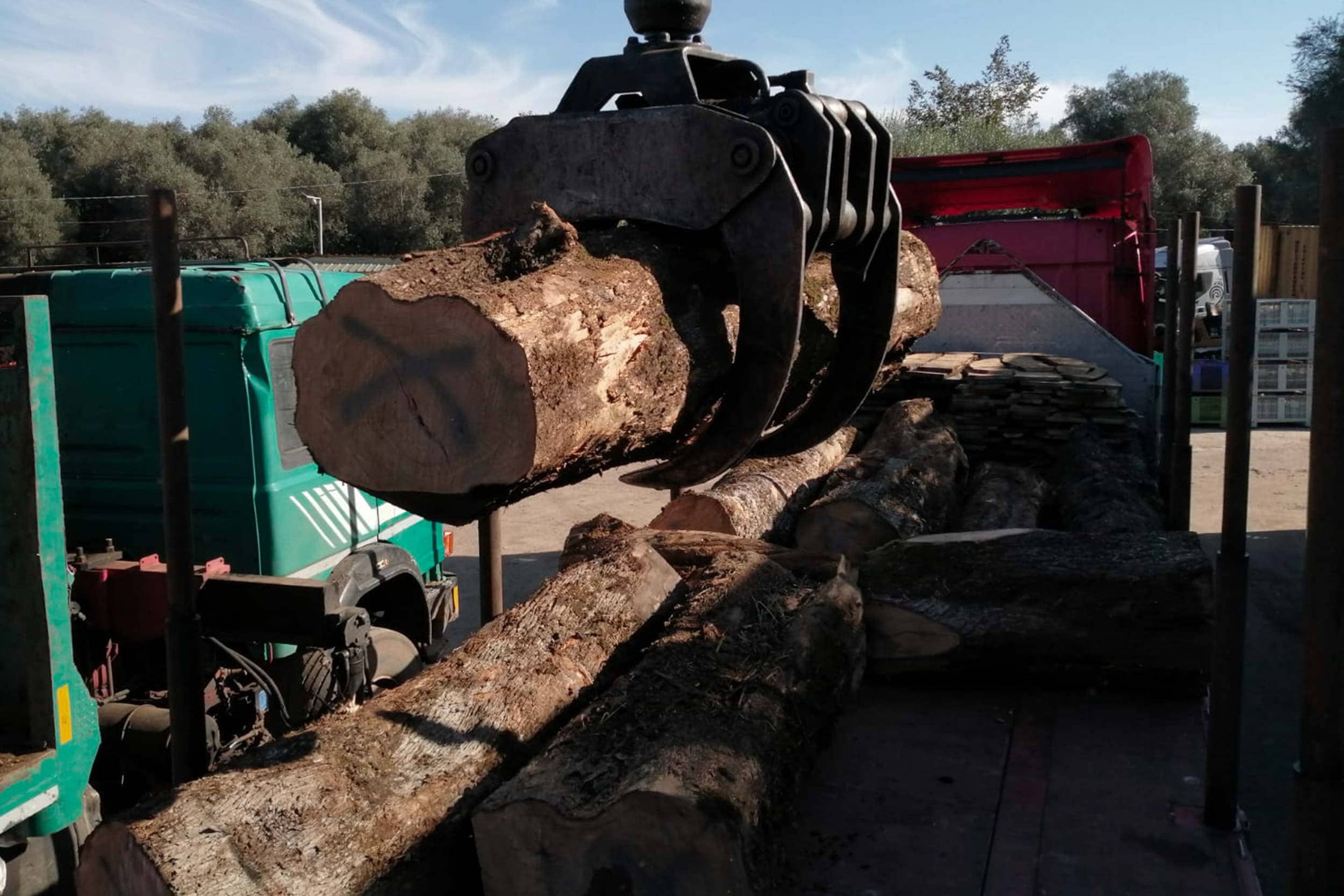
To start with I need to find quality trees because not every Olive tree has necessarily interesting wood to work on.
I recuperate the branches, stumps, or trunks, that are also known as olive logs, in various countries such as France, Spain, Italy and sometimes even further afar, according to the hazards of climates (for example damage caused by frost).
The logs are then rapidly cut into planks or into blocks according to the desired objects. The planks are stocked flat, outside for 8 to 10 years before being used to create objects.
On the other hand, salad bowls and bowls are shaped as quickly as possible in green wood, then dried for 3 years according to a unique technique which has been certified by the Ministry of Economy. (“EPV- Entreprise du Patrimoine Vivant” – Living Heritage Company).
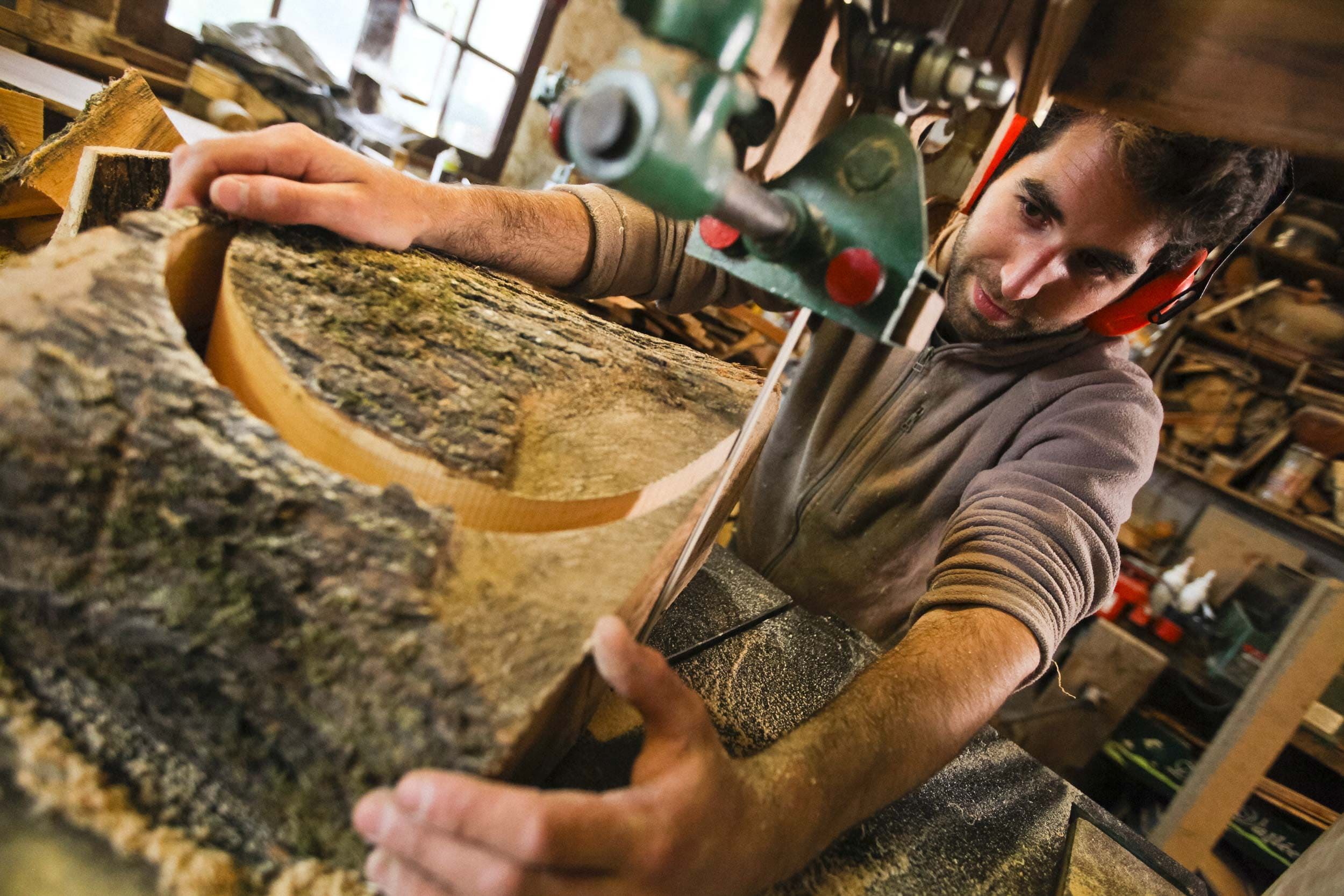
The logs are then rapidly cut into planks or into blocks according to the desired objects. The planks are stocked flat, outside for 8 to 10 years before being used to create objects.
On the other hand, salad bowls and bowls are shaped as quickly as possible in green wood, then dried for 3 years according to a unique technique which has been certified by the Ministry of Economy. (“EPV- Entreprise du Patrimoine Vivant” – Living Heritage Company).
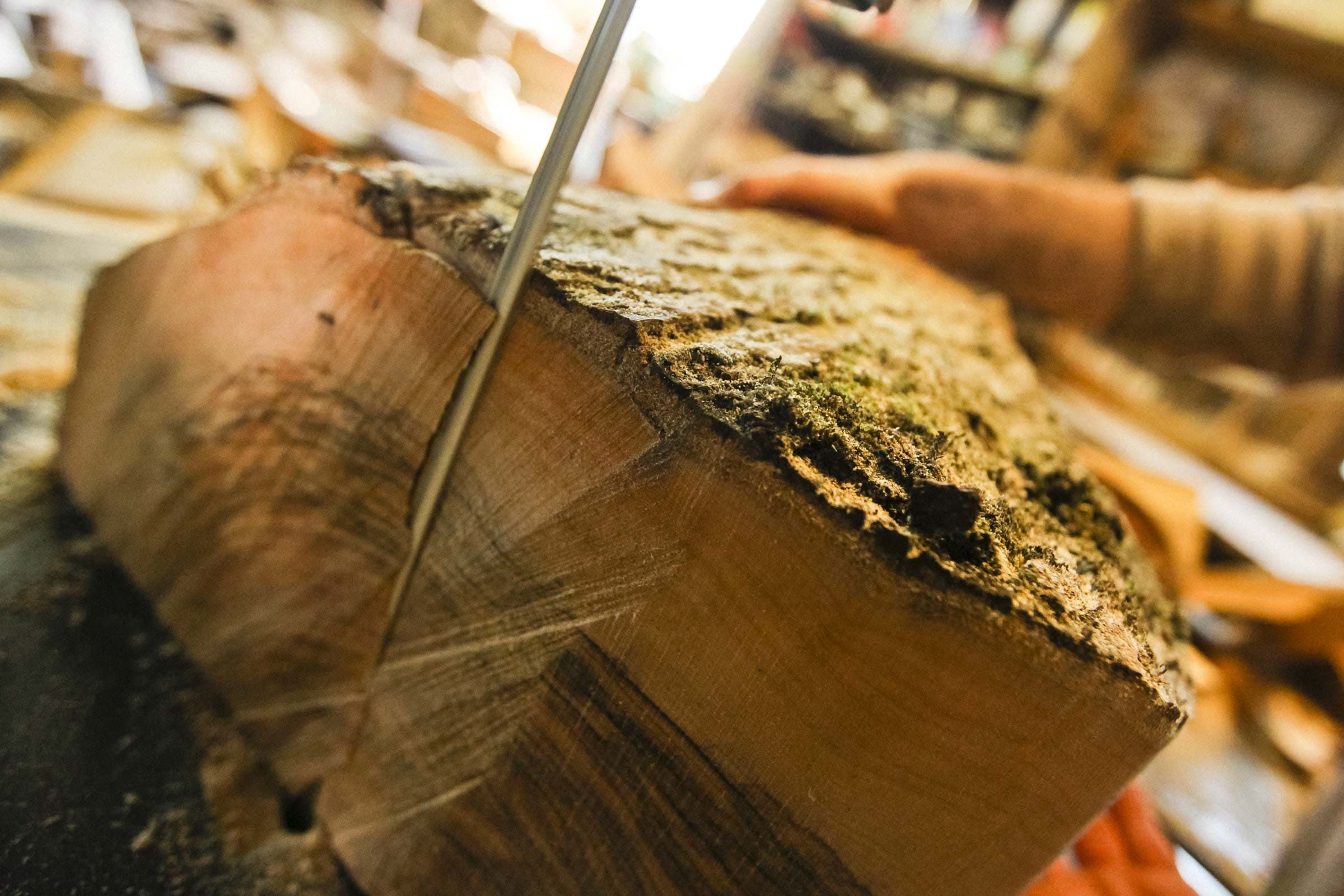
I start by creating the larger objects, such as salad bowls which require first quality wood.
Then, using the scraps I undertake to create various other objects until I obtain just tiny pieces of wood that I use to fill various cracks or faults.
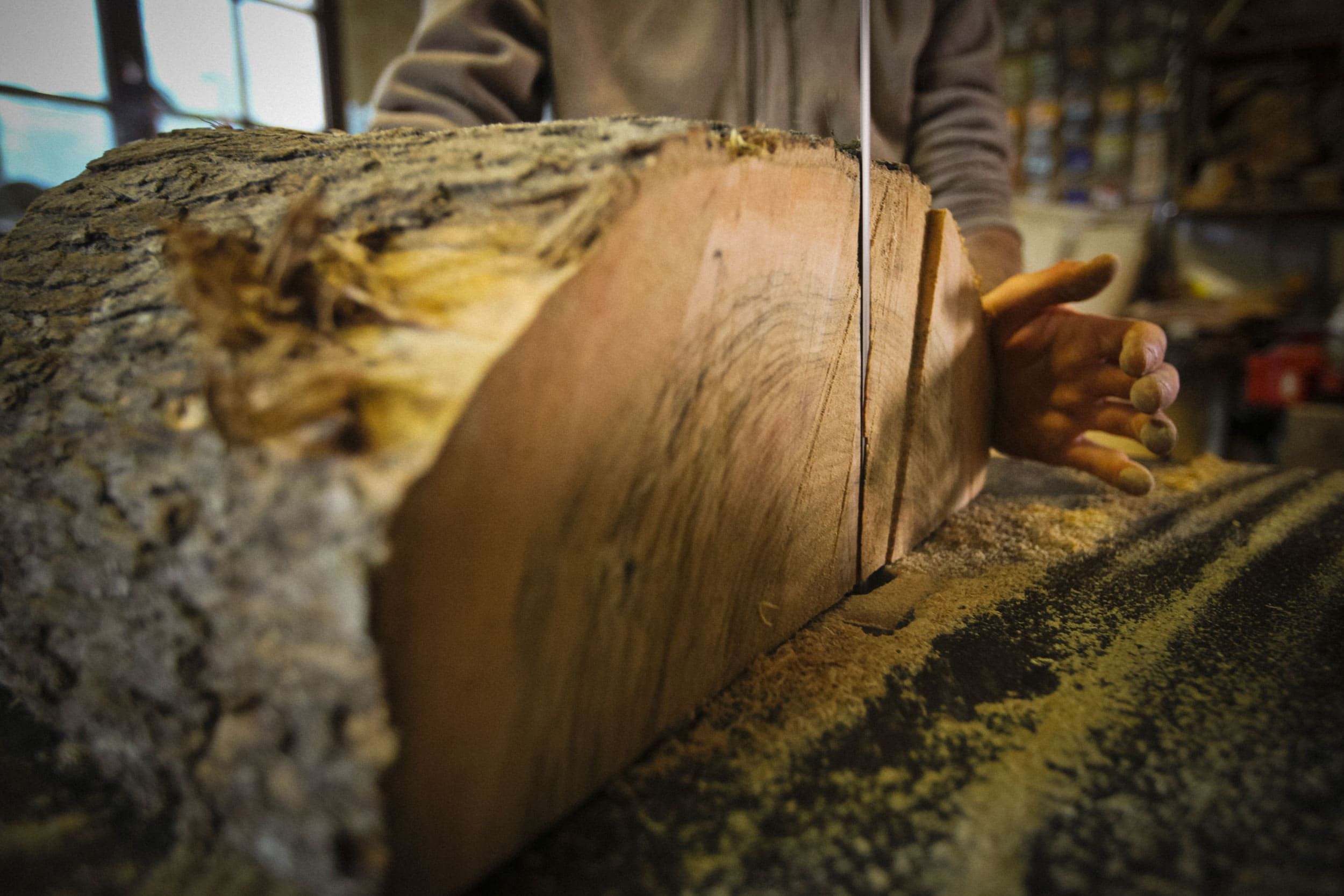
A few years ago the shavings collected during the hollowing placed a serious problem of volume which I solved by installing a wood chip boiler. By doing this I am totally autonomous today in matters of heating throughout the whole winter.
Olive woodwork requires most of the tools that are used in carpentry and cabinet making such as: a band saw, jointer, planer, wood chisels, belt sander etc.
However, for much of the work on olive wood, it is indispensable to create our own tools or machines as other professions using wood to not respond to the same requirements.
Effectively, I use various known machines, but all the tools must be sharpened according to the angles we have elaborated with my father. The rotation speed or material flow have been studied to improve the efficacy of the shaping of the wood and the quality of my confections.
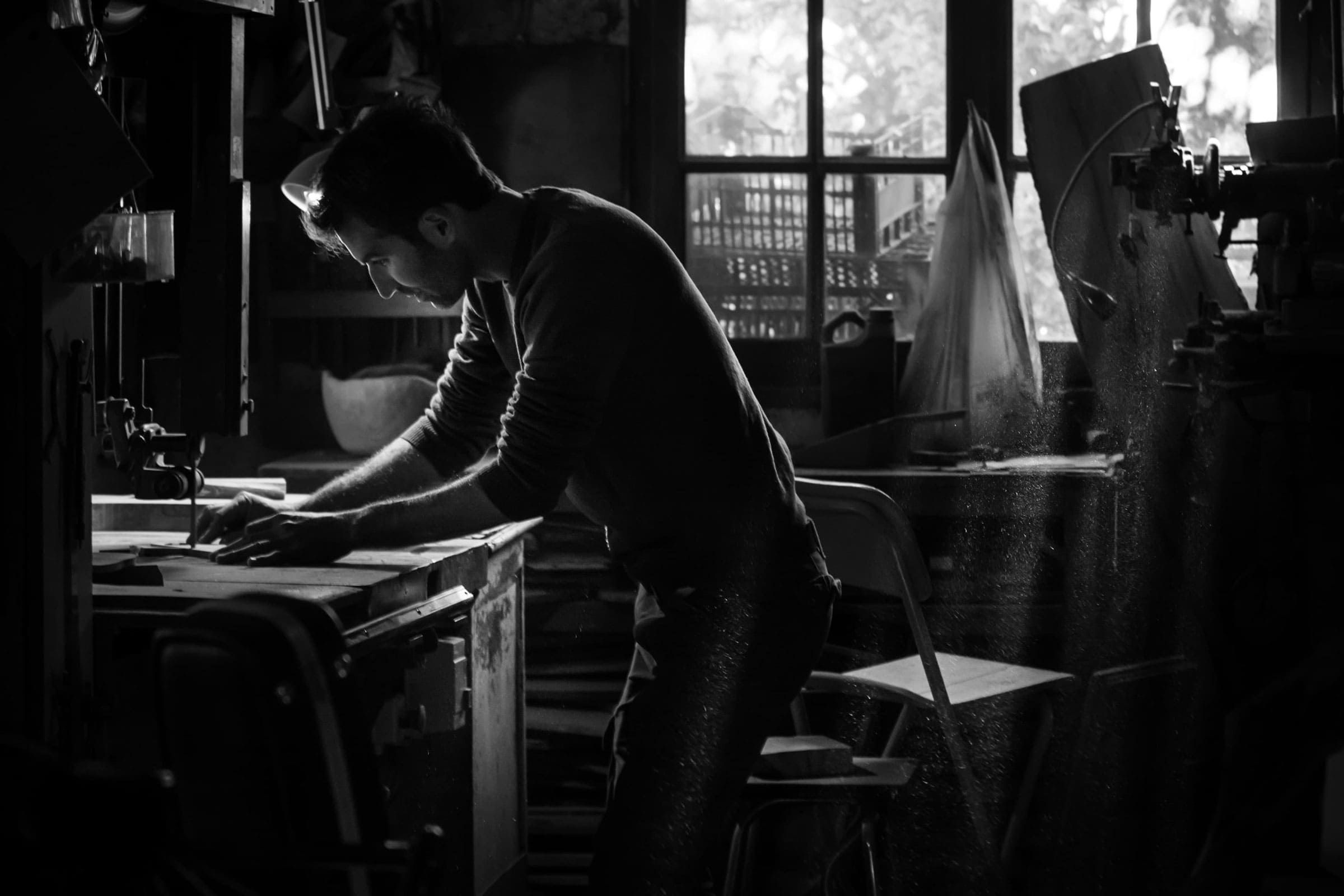
Olive woodwork requires most of the tools that are used in carpentry and cabinet making such as: a band saw, jointer, planer, wood chisels, belt sander etc.
However, for much of the work on olive wood, it is indispensable to create our own tools or machines as other professions using wood to not respond to the same requirements.
Effectively, I use various known machines, but all the tools must be sharpened according to the angles we have elaborated with my father. The rotation speed or material flow have been studied to improve the efficacy of the shaping of the wood and the quality of my confections.
It is well known that machines can never totally replace the hands of men. For many steps, I enjoy using tools such as hollow chisels, an adze, small axes, and paint brushes for the finishing details. A craftsman’s eye is irreplaceable because only he can decide on seeing his material, the object to create.
My father often used to say :
“A hand made object is above all a head made object.”
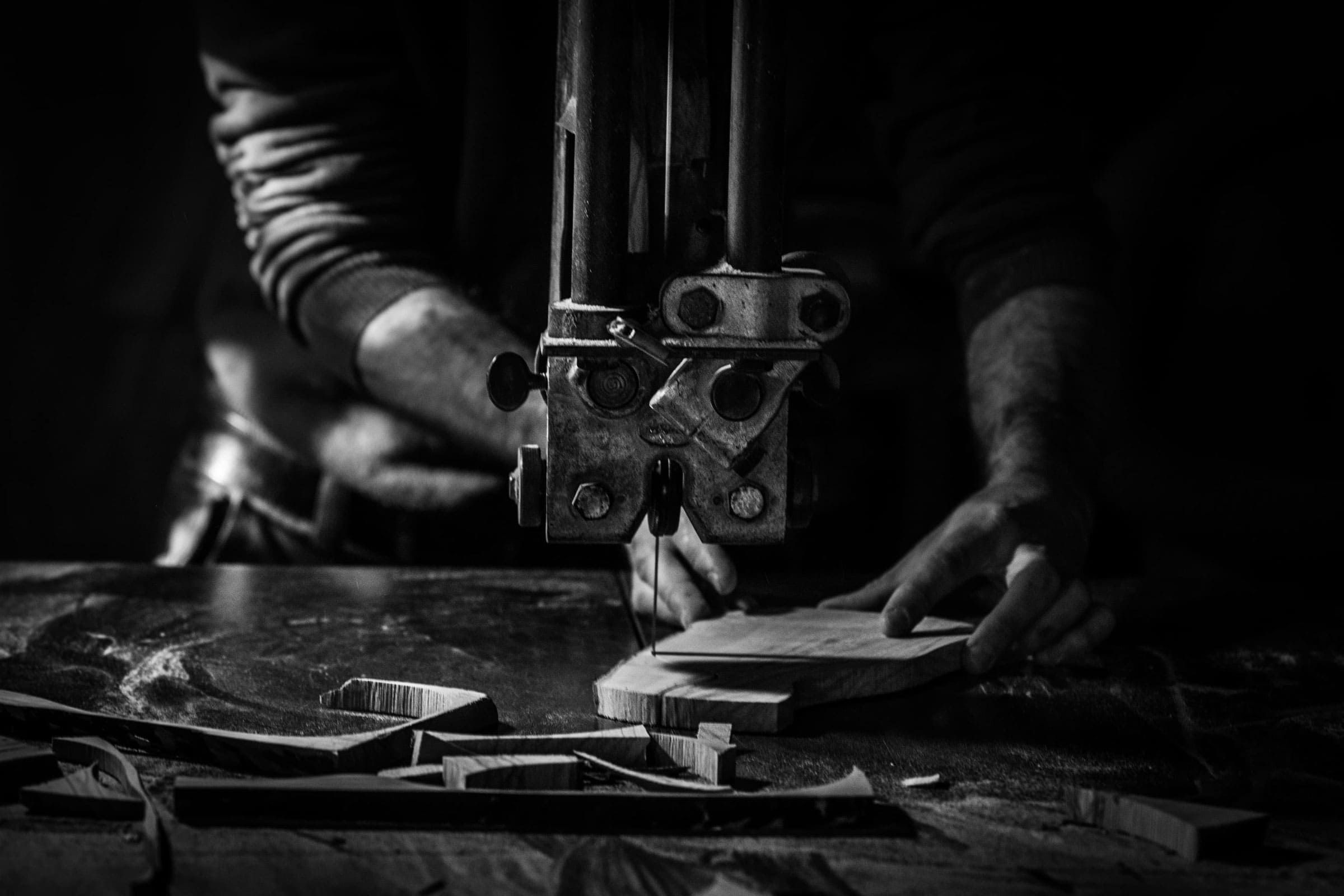
It is well known that machines can never totally replace the hands of men. For many steps, I enjoy using tools such as hollow chisels, an adze, small axes, and paint brushes for the finishing details. A craftsman’s eye is irreplaceable because only he can decide on seeing his material, the object to create.
My father often used to say :
“A hand made object is above all a head made object.”